The Railing
Have you ever taken a moment to think about handrails? They are everywhere. They help us on stairways and steep inclines. They can be fancy or simple. They can act as a barrier between safe and unsafe areas. Upon further investigation, these seemingly common structures turn out to be rather complex.
In an offshore environment, railings are fundamental in keeping service technicians safe whilst at work in harsh and unpredictable conditions high above the water.
Beyond this, they also have to withstand dynamic loading, chemical exposure, temperature extremes and vibration. They will continuously be exposed to harsh saltwater conditions and prolonged UV radiation and have to support the weight of the equipment mounted to withstand blunt force impact.
It’s easy to take the railing for granted but the process of designing and producing such a railing is complex. For starters, what material should be used? How will it fit to the structure? Will it handle the forces stressed upon it? Where will it be assembled?
Furthermore, thought must be given to access points, hooking points, cable routing and mounting components.
So the railing, this seemingly minor facet of offshore wind platform construction, requires a lot more consideration, and investment than at first thought.

Welded & Rivetted
Weissenborn has made a name for itself making welded aluminum railings for offshore wind. With a long history and skilled welders on staff, the company has built an expertise that it is putting to good.
Throughout its development, Weissenborn has wondered if there might be a more efficient way to make railings. This thought process and project experience led to the development of railings based on riveted technology, the new EverSafe System™
EverSafe ® System
Weissenborn’s patented EverSafe System aims to simplify the railing experience by reducing the design complexity and production cost of a rail system, without compromising safety.
Its modular design uses standardized parts in a building block concept for quick and easy construction, transportation and installation.
EverSafe uses rivets instead of traditional welding which avoids extra time, expense and documentation work. Manufactured with marine grade aluminum it is a durable yet lightweight solution providing unbeatable corrosion protection and flexibility.
You are currently viewing a placeholder content from Vimeo. To access the actual content, click the button below. Please note that doing so will share data with third-party providers.
More Information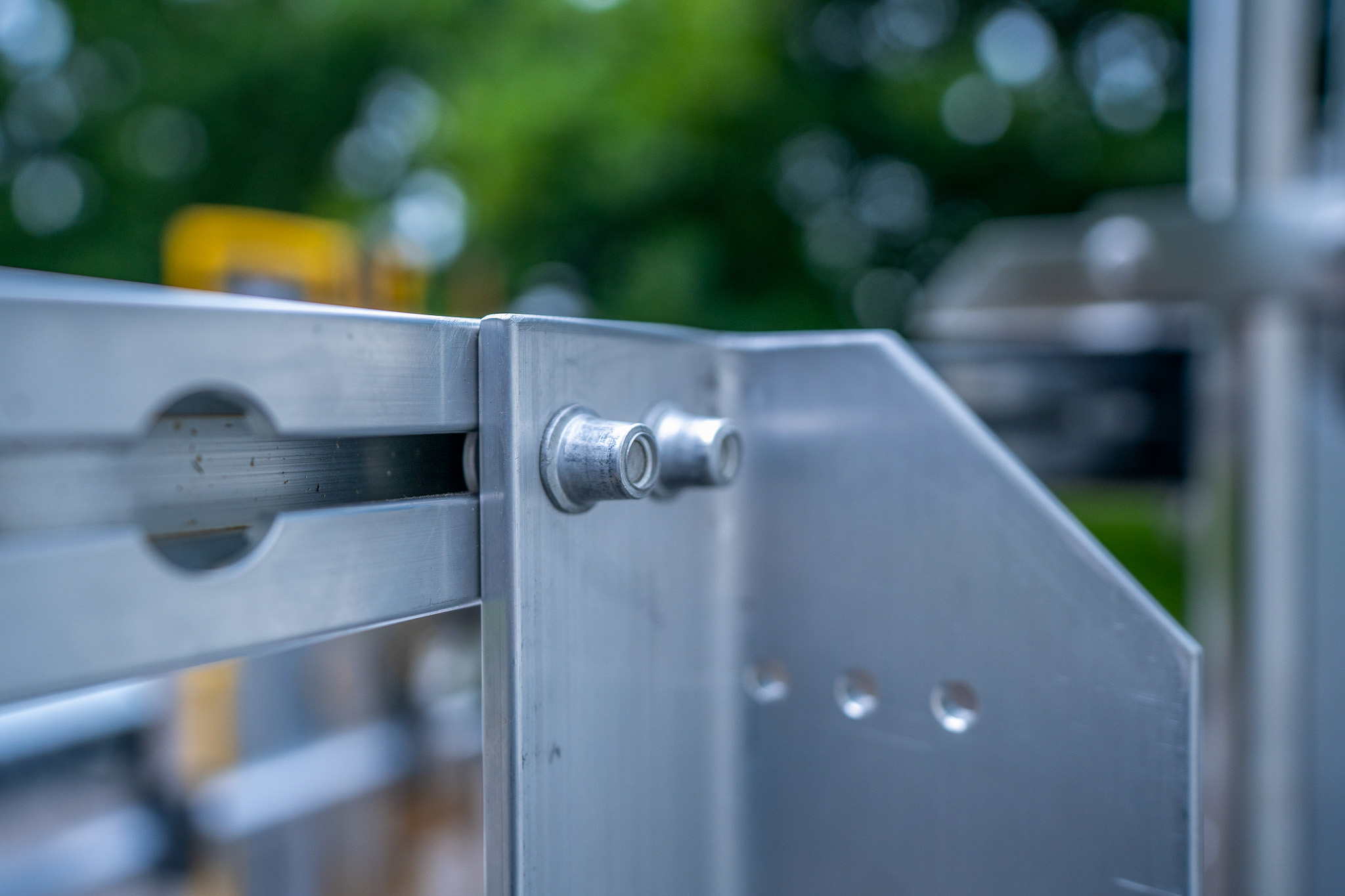


EverSafe uses Rivets
Riveting technology has been successfully used in industrial applications for a long time. It’s strong enough to hold bridges, planes, and even spacecraft together.
So why not railings?
Using rivets brings many advantages in strength and simplicity, this is why Weissenborn has brought rivets to railings.
Simplicity of the connection
The unique connection created by a rivet holds against vibration, an advantage over bolting. Unlike welding which has to heat the alloy, the rivet connection is cold, thus not changing the material composition of the metal.
Simplicity in construction
A simple pneumatic or electric tool is used to assemble the EverSafe System. There is no need for highly skilled labor to weld pieces together. Entire systems can be assembled in minutes, instead of hours and savings on time means savings on labor costs.
Resistant to vibration
Riveted connections offer distinct advantages over bolts, particularly in terms of vibration resistance. Unlike bolts, rivets create a permanent connection that cannot be easily loosened and redone. The tight fit achieved through the riveting process contributes to a stronger connection, distributing and absorbing vibrations effectively. This enhanced strength helps in minimizing the risk of fatigue caused by cyclic loading. Vibrations, a common concern in structural elements, can gradually loosen fasteners over time, posing a potential threat in bolted connections. In contrast, the inherent permanence of riveted joints renders them less susceptible to loosening under vibrational loads, ensuring a more resilient and durable connection.
It’s Aluminum
Choice of material is particularly important in meeting the demanding environment and requirements of the offshore wind industry. Aluminum provides a lightweight, durable and corrosion resistant solution.
The high strength-to-weight ratio of aluminum enables the construction of structures that can withstand substantial loads, all while maintaining a comparatively low-weight product for easier and cost-efficient transportation and installation.
Aluminum boasts a natural corrosion resistance attributed to its passive oxide layer, a transparent film formed when exposed to air. Composed mainly of aluminum oxide, this layer acts as a protective barrier, preventing further oxidation and corrosion. Notably, the oxide layer is self-renewing, which helps maintain the metal’s corrosion resistance.
It’s Green
Repurposing previously used materials in new products plays a vital role in fostering a circular economy and reducing the environmental impact on Earth.
This isn’t just about manufacturing a product; it’s a conscious effort to build a more sustainable future.
The aluminum we use to manufacture the EverSafe System is made from 70% recycled material. Producing recycled aluminum only takes around 5% of the energy needed to make new aluminum — thus significantly reducing carbon emissions.
The modular design of EverSafe allows for more compact and efficient transportation compared to welded segments (for perspective, 13 EverSafe kits can fit into a 40′ container versus only 4 welded sets), thereby minimizing transport requirements and reducing the associated carbon footprint.
It’s User-friendly
The EverSafe System is designed with a unique approach to ensure that it’s simple and adaptable for construction projects worldwide. Unlike traditional methods which rely on specialist welding skills and facilities, we provide the system in a convenient kit form, easy for anyone to assemble at local construction sites.
The modular railing kits are designed to streamline construction and installation whilst our step-by-step manuals offer clear, straightforward instructions, simplifying the assembly process.
Each wind farm project using the EverSafe System benefits from its own assembly table, facilitating a smooth and organized workflow. The assembly itself requires a simple pneumatic tool, eliminating the need for specialized or highly skilled labor.
This user-friendly design ensures that anyone, regardless of expertise, in any location, can easily and quickly assemble the system, making it truly versatile for the global offshore wind industry.
You are currently viewing a placeholder content from Vimeo. To access the actual content, click the button below. Please note that doing so will share data with third-party providers.
More Information… and more
Our expertise extends beyond welding. We harness our knowledge and experience to design not only railing systems but also integrate low voltage electrical design. Combining these two streamlines the project design process, effectively reducing potential interface problems that can lead to costly project delays.
This holistic approach not only enhances the efficiency of the design phase but also translates to a smoother execution in the production phase. Our commitment to integrating processes underscores our dedication to innovation and excellence in serving the offshore wind industry.
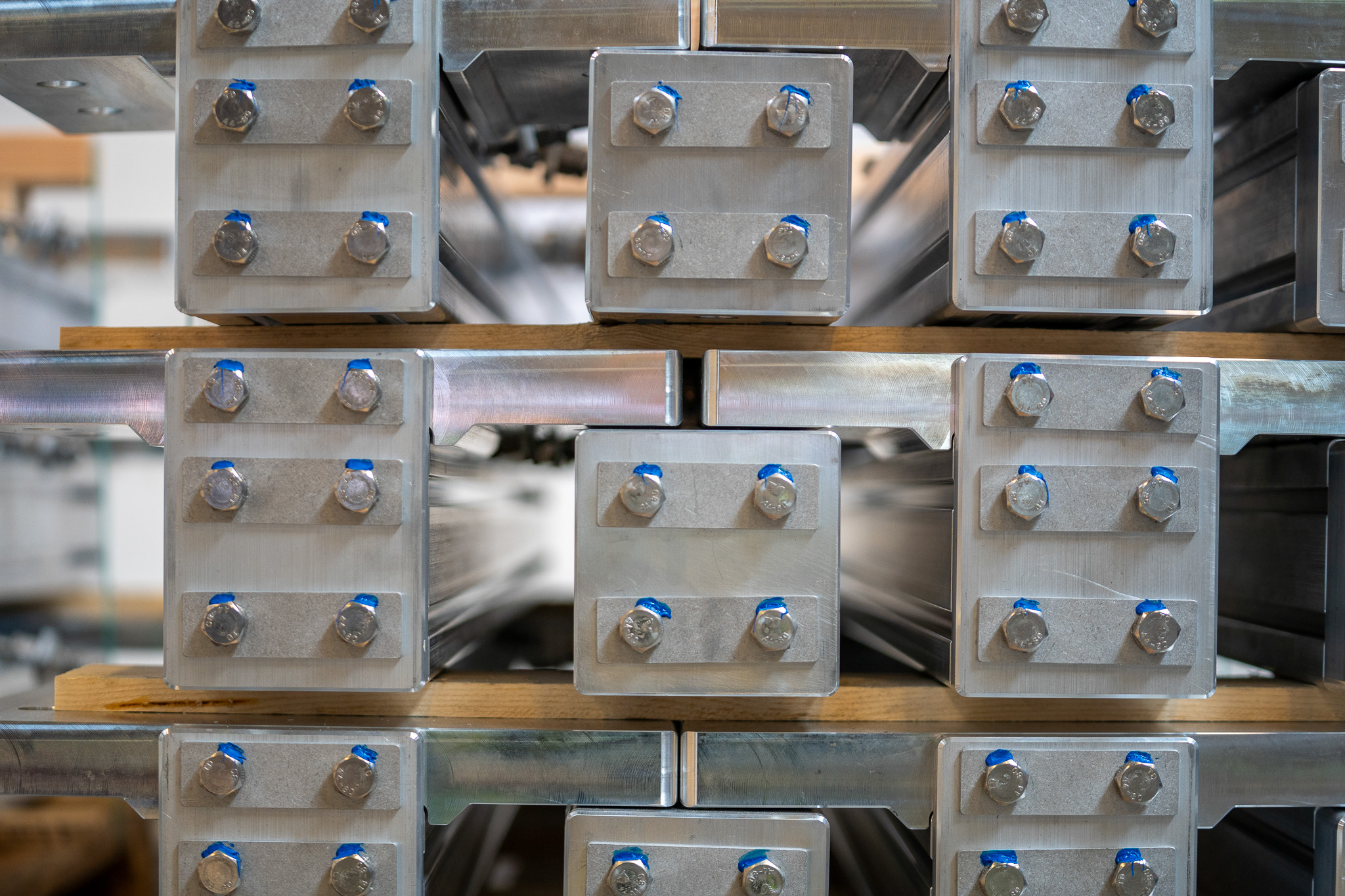
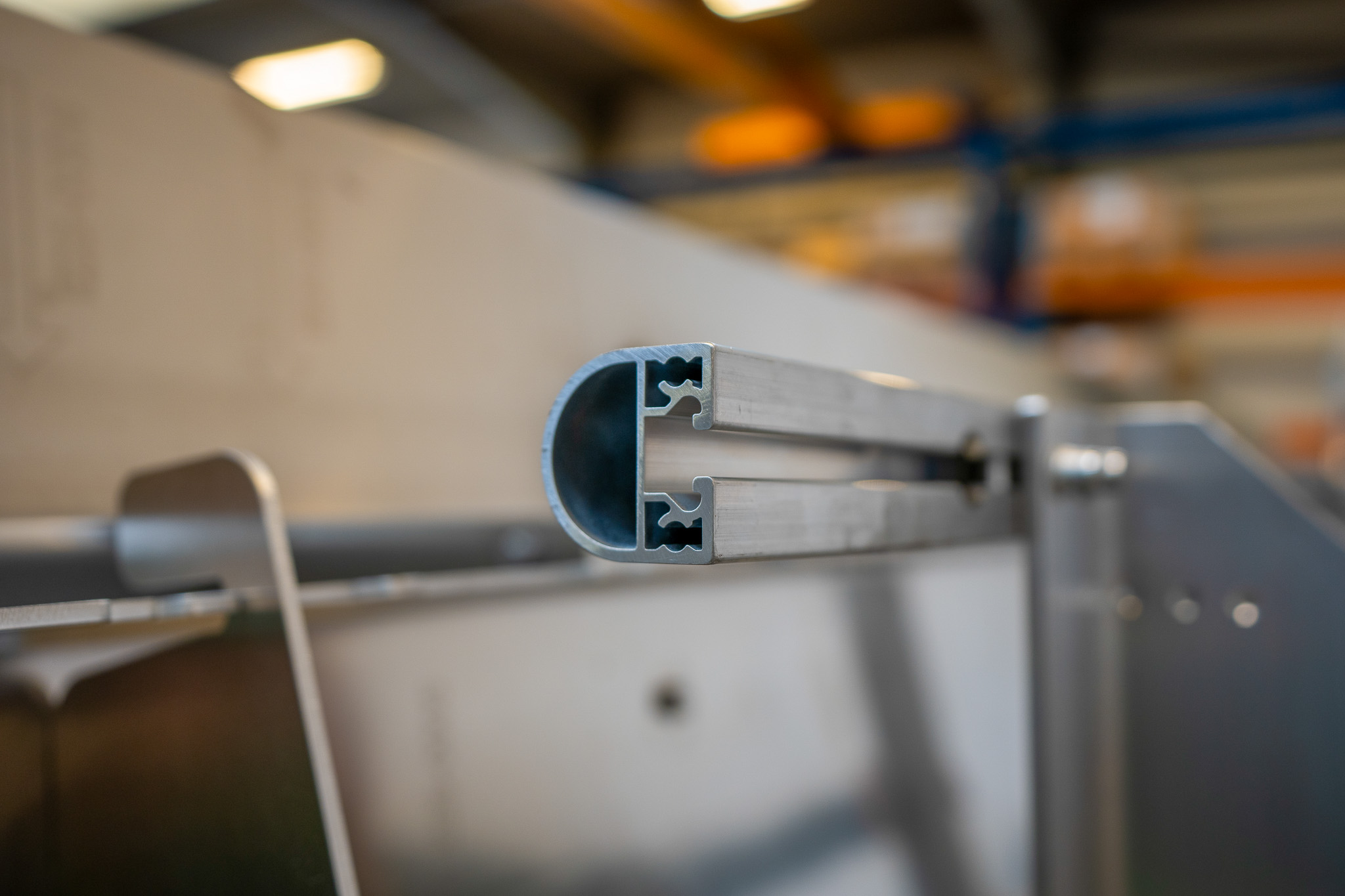
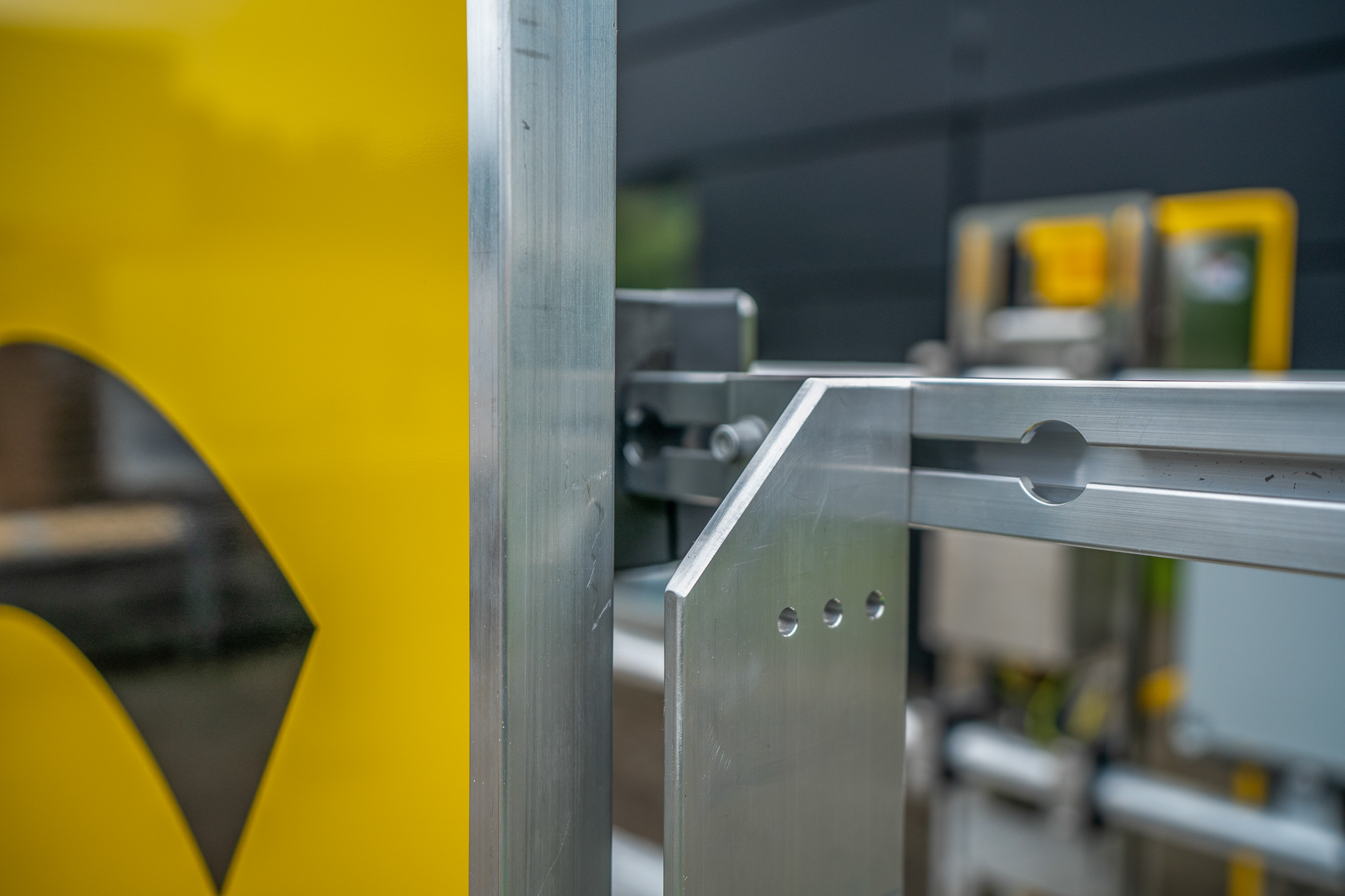